荆州电液动装车闸门 DYDZ矸石仓防窜仓装车闸门
浏览次数:104次
- 产品规格:
- 发货地:江苏省扬州高邮市
关键词
荆州电液动装车闸门
详细说明
九、液压站的维护与保养
1.设备及周围环境应经常清扫干净。
2.对油箱内的油液应经常进行过滤检查,若发现油液不能满足系统工作要求时,应及时更换(维护好时一般一年更换一次,以保证系统正常运行)。
3.每次注油需采用10μm精度的加油滤油车经空气滤清器加入,确
保液压系统清洁度达到NAS8级。应经常检查油箱上的油标,如发现液位在油标以下,应及时检查漏油原因并补充油液。
4.油过滤器的更换以油过滤器的堵塞情况而定,指针显示式过滤器分绿、黄、红三个区域,油泵停止运行时指针位于绿区表示正常,位于黄区表示轻微堵塞,位于红区但接近黄区则表示堵塞,位于红区并远离黄区则表示严重堵塞,油泵停止运行时指针位于红区内就应更换滤油器滤芯。
5.经常定期检查各部分管接头、接合面,对渗油处应及时查找原因,更换密封件(建议每周检查一次),并经常进行检查、紧固。
6.经常定期检查各液压管路上的管夹螺钉是否松动,并及时拧紧。(建议每周检查一次)
7.经常定期检查各液压阀组的结合面是否渗液,对渗油处应及时查找原因,或更换密封件或及时拧紧。(建议每周检查一次)
8.液压设备大修时,一般情况不允许拆开泵、阀等主要液压元件的零件,有条件的情况下可进行拆装检查,但组装后一定要上试验台试验,确认满足设计要求之后方可使用,否则应更换。
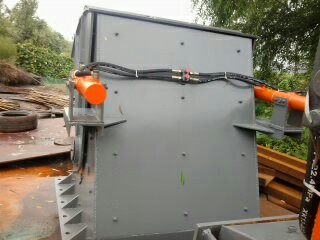
八、系统的调试与试运转
液压系统安装完毕后,首先根据液压系统原理图、各部分施工设计图、电气设计图等检查安装是否正确无误,否则应及时处理。
系统的调试与试运转应有现场的操作及维修人员参加,首先应熟悉液压系统的构造、性能、技术文件。
系统的调试一般应按泵站调试、系统调试(包括压力和流量的调试)的顺序进行,各调试项目均由部分到系统整体逐项进行,即部件、单机、区域联动、机组联动等。主液压泵 A10VS0140DFR泵(见图四)调试步骤
1)将泵上的恒压阀和系统溢流阀压力均调解到小(泵上的流量阀在油泵生产厂家出厂时已调好),即零压,启泵。
2)将泵上的恒压阀压力调到,即往里顶到再往回松1.5圈,此时系统的溢流阀压力还是小。
3)将系统溢流阀压力往上调,分别调到50、100、150bar并同时观察
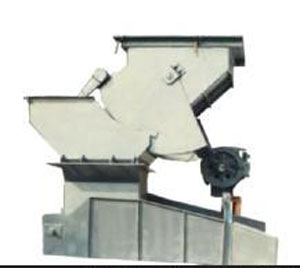
4、试起动:起动前先点动电机,确认电机的旋向和标志箭头方向一致后,方可起动电机,然后按下闸门开、关按纽,让闸门在无负载下工作数个来回(约15秒),以排尽管路中的空气,使蓄能器内的充油压力和系统设定压力一致后(系统设定为7Mpa),然后才能进入预备工作状态。
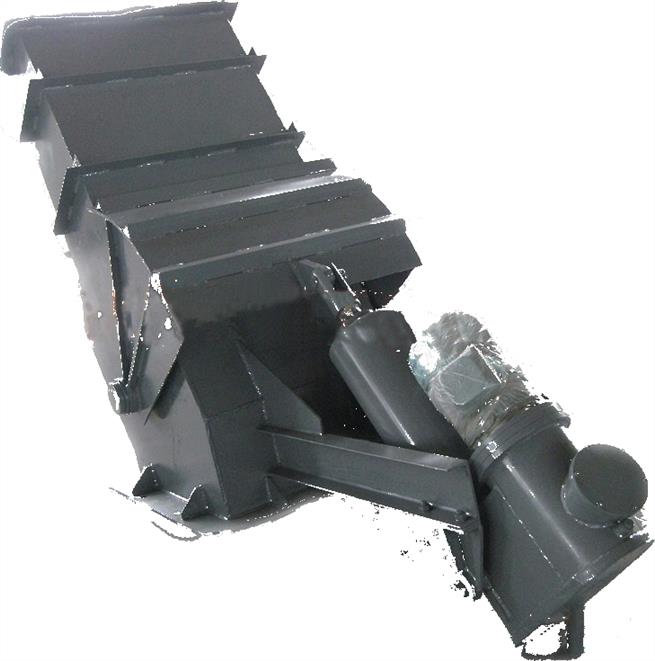
11.管道直管部分的支架距离应符合下表的规定:
直管外径
(mm) ≤10 10~25 25~50 50~80 >80
支架间距
(mm) 500~1000 1000~1500 1500~2000 2000~3000 3000~5000
12.高压软管的安装应符合下列规定:
1) 应避免急弯,外径大于30mm的软管,其小弯曲半径不应小
于管子外径的9倍,外径小于等于30mm的软管,其小弯曲半径不应小于管子外径的7倍。
2)与管接头的连接处,应有一段直线过渡部分,其长度应不小于管
子外径的6倍。
3) 当长度过长或受急剧振动时,应用管卡夹牢,但应尽量少用。
4) 当自重会引起过大变形时,应设支托。
5) 软管长度除满足弯曲半径和移动行程外,尚应留有4%的余量。
6) 软管相互间及同其它物件不得磨擦。
13.试组装完成后,将各钢管路拆下,再次进行酸洗、钝化,清除管内氧化皮,达到防锈的效果。
14.液压系统管道在安装位置上组成循环冲洗回路时,先将各部分管路串联成一条循环管路,应将液压油缸、液压阀和蓄能器与冲洗回路分开,将各阀组管口再次封好,然后,采用设备上的冲洗油泵对总管路进行70小时以上时间的冲洗。冲洗压力不高于1MPa、流量达到值,冲洗过程中要经常对各钢管路进行敲击,以便加速附着在钢管上杂物的脱落,并经常观察10μ精度的压力管路滤油器是否堵塞。冲洗时间达到70小时后,在10μ精度的压力管路滤油器后边抽取油样进行化验,在确认系统内达到NAS8级清洁度之后方可停止管路冲洗。
15.管道冲洗完成后,当要拆卸接头时,应立即封口,当需对管口焊接处理时,对该管道应重新进行酸洗和冲洗。
16.抽净油箱内的液体,用合好的面团沾净油箱内的污物。
17.液压钢管的涂面漆应在试压合格之后进行,涂层应均匀、完整、和漏涂,漆膜应附着牢固、无剥落、无、无气泡等缺陷。
18.按系统要求,联接好各液压管路,各液压阀组块与管路的联接应以阀组块上的P、T、L、A、B等标记或阀组块图纸为准,并进行检查确认。
m.jan885566.b2b168.com
1.设备及周围环境应经常清扫干净。
2.对油箱内的油液应经常进行过滤检查,若发现油液不能满足系统工作要求时,应及时更换(维护好时一般一年更换一次,以保证系统正常运行)。
3.每次注油需采用10μm精度的加油滤油车经空气滤清器加入,确
保液压系统清洁度达到NAS8级。应经常检查油箱上的油标,如发现液位在油标以下,应及时检查漏油原因并补充油液。
4.油过滤器的更换以油过滤器的堵塞情况而定,指针显示式过滤器分绿、黄、红三个区域,油泵停止运行时指针位于绿区表示正常,位于黄区表示轻微堵塞,位于红区但接近黄区则表示堵塞,位于红区并远离黄区则表示严重堵塞,油泵停止运行时指针位于红区内就应更换滤油器滤芯。
5.经常定期检查各部分管接头、接合面,对渗油处应及时查找原因,更换密封件(建议每周检查一次),并经常进行检查、紧固。
6.经常定期检查各液压管路上的管夹螺钉是否松动,并及时拧紧。(建议每周检查一次)
7.经常定期检查各液压阀组的结合面是否渗液,对渗油处应及时查找原因,或更换密封件或及时拧紧。(建议每周检查一次)
8.液压设备大修时,一般情况不允许拆开泵、阀等主要液压元件的零件,有条件的情况下可进行拆装检查,但组装后一定要上试验台试验,确认满足设计要求之后方可使用,否则应更换。
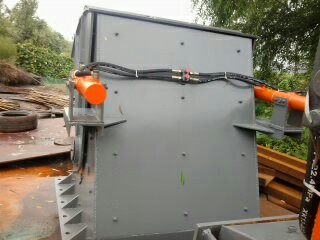
八、系统的调试与试运转
液压系统安装完毕后,首先根据液压系统原理图、各部分施工设计图、电气设计图等检查安装是否正确无误,否则应及时处理。
系统的调试与试运转应有现场的操作及维修人员参加,首先应熟悉液压系统的构造、性能、技术文件。
系统的调试一般应按泵站调试、系统调试(包括压力和流量的调试)的顺序进行,各调试项目均由部分到系统整体逐项进行,即部件、单机、区域联动、机组联动等。主液压泵 A10VS0140DFR泵(见图四)调试步骤
1)将泵上的恒压阀和系统溢流阀压力均调解到小(泵上的流量阀在油泵生产厂家出厂时已调好),即零压,启泵。
2)将泵上的恒压阀压力调到,即往里顶到再往回松1.5圈,此时系统的溢流阀压力还是小。
3)将系统溢流阀压力往上调,分别调到50、100、150bar并同时观察
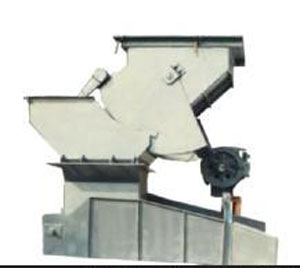
4、试起动:起动前先点动电机,确认电机的旋向和标志箭头方向一致后,方可起动电机,然后按下闸门开、关按纽,让闸门在无负载下工作数个来回(约15秒),以排尽管路中的空气,使蓄能器内的充油压力和系统设定压力一致后(系统设定为7Mpa),然后才能进入预备工作状态。
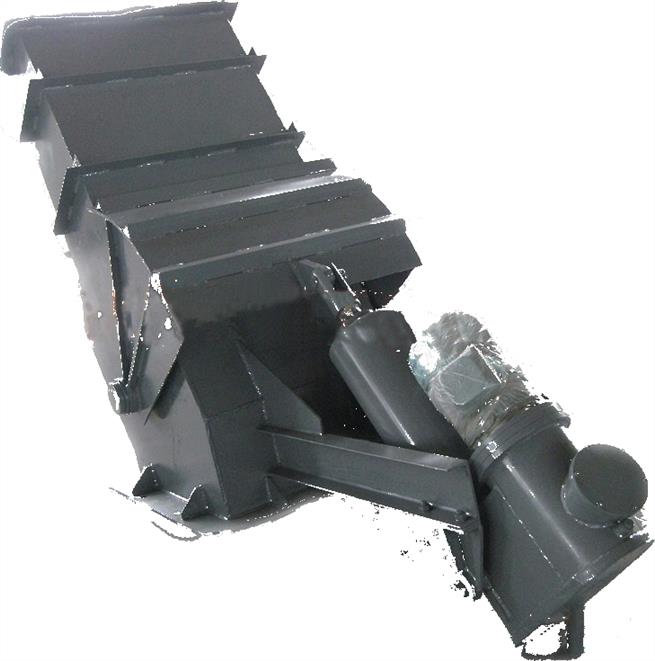
11.管道直管部分的支架距离应符合下表的规定:
直管外径
(mm) ≤10 10~25 25~50 50~80 >80
支架间距
(mm) 500~1000 1000~1500 1500~2000 2000~3000 3000~5000
12.高压软管的安装应符合下列规定:
1) 应避免急弯,外径大于30mm的软管,其小弯曲半径不应小
于管子外径的9倍,外径小于等于30mm的软管,其小弯曲半径不应小于管子外径的7倍。
2)与管接头的连接处,应有一段直线过渡部分,其长度应不小于管
子外径的6倍。
3) 当长度过长或受急剧振动时,应用管卡夹牢,但应尽量少用。
4) 当自重会引起过大变形时,应设支托。
5) 软管长度除满足弯曲半径和移动行程外,尚应留有4%的余量。
6) 软管相互间及同其它物件不得磨擦。
13.试组装完成后,将各钢管路拆下,再次进行酸洗、钝化,清除管内氧化皮,达到防锈的效果。
14.液压系统管道在安装位置上组成循环冲洗回路时,先将各部分管路串联成一条循环管路,应将液压油缸、液压阀和蓄能器与冲洗回路分开,将各阀组管口再次封好,然后,采用设备上的冲洗油泵对总管路进行70小时以上时间的冲洗。冲洗压力不高于1MPa、流量达到值,冲洗过程中要经常对各钢管路进行敲击,以便加速附着在钢管上杂物的脱落,并经常观察10μ精度的压力管路滤油器是否堵塞。冲洗时间达到70小时后,在10μ精度的压力管路滤油器后边抽取油样进行化验,在确认系统内达到NAS8级清洁度之后方可停止管路冲洗。
15.管道冲洗完成后,当要拆卸接头时,应立即封口,当需对管口焊接处理时,对该管道应重新进行酸洗和冲洗。
16.抽净油箱内的液体,用合好的面团沾净油箱内的污物。
17.液压钢管的涂面漆应在试压合格之后进行,涂层应均匀、完整、和漏涂,漆膜应附着牢固、无剥落、无、无气泡等缺陷。
18.按系统要求,联接好各液压管路,各液压阀组块与管路的联接应以阀组块上的P、T、L、A、B等标记或阀组块图纸为准,并进行检查确认。
m.jan885566.b2b168.com